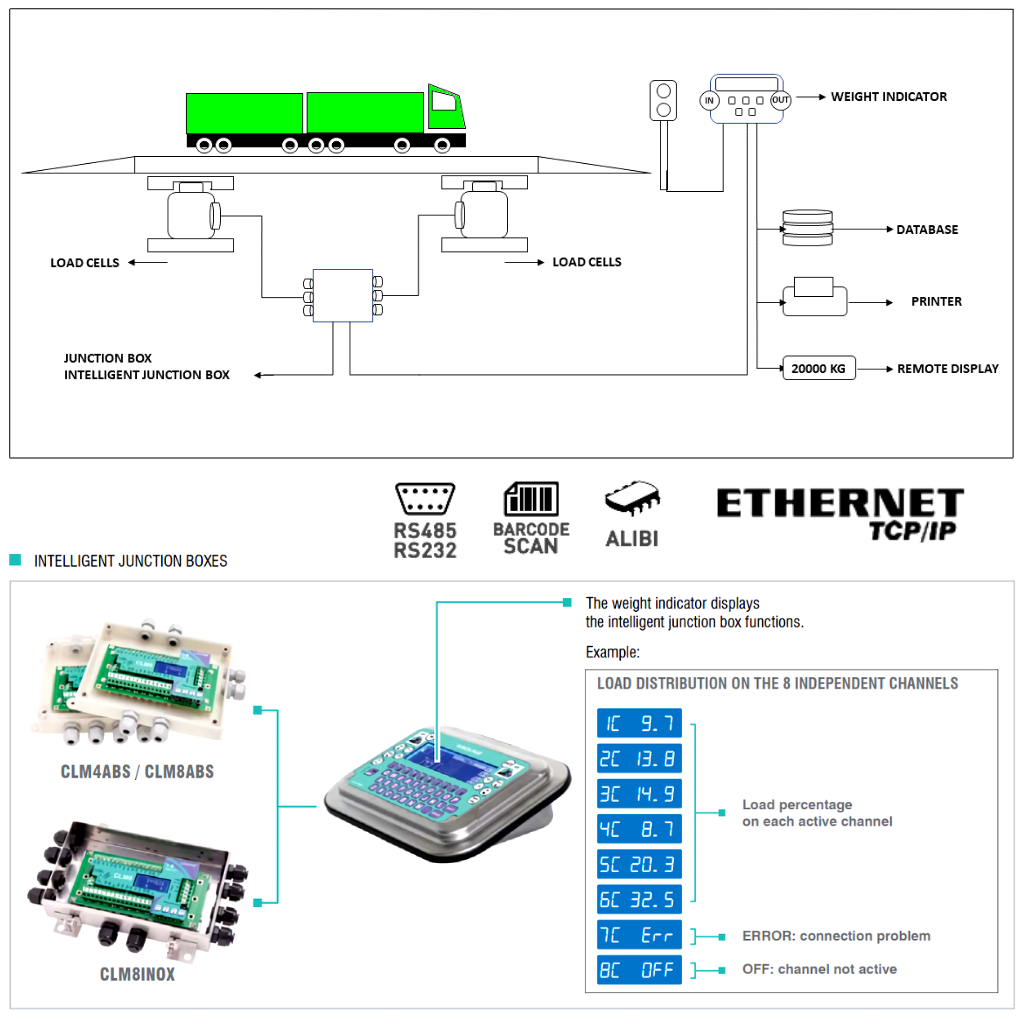
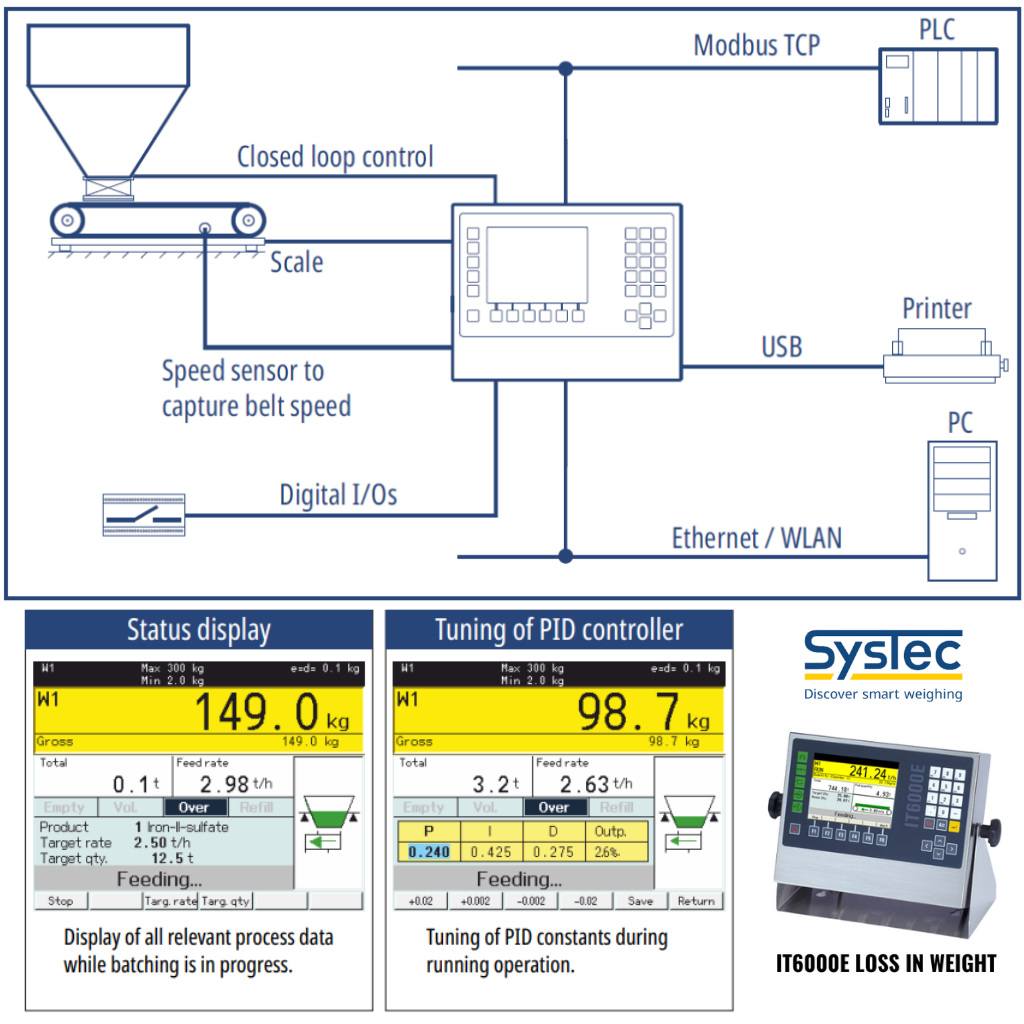
Intelligent PID controller
Recording of up to 10 feed rate curves for volumetric operation with fill-level related correction functionality.
Security
- Power-fail-safe storage of data
- Password protection for all data
- Battery-backed real-time clock
- Plain text display of error messages.
Ex2/22 version
For installation in Ex zones 2 and 22.
SysTec IT6000E, Weighing Indicator for Loss in Weight Application
The Industrial Weighing Terminal
- IT6000E LOSS IN WEIGHT is a controller for loss-in-weight weighing systems used for the discharging of bulk material in continuous processes for food, chemical products, building materials and other sectors of industry
- IT6000E LOSS IN WEIGHT connects to analog or digital scales of all types, including Ex-area applications.
- IT6000E LOSS IN WEIGHT is suited for the continuous supply of product to
- Extruders
- Injection die casting machines
- Continuous mixers
- And other process equipment requiring constant material flow.
- The raw material is discharged at constant flow rate from the weigh hopper via screw, vibratory or rotary feeder.
- IT6000E LOSS IN WEIGHT controls the feeding device to adjust the actual feed rate to the preset target. The automatic refilling of the weigh hopper is controlled via selectable setpoints and takes place without interrupting the feeding process.
- The current process status is indicated on the clearly arranged color display. The most important features are:
- Raw material file for 15 products to store the material-related batching parameters
- Selection of product via display/keyboard or external inputs
- Gravimetric or volumetric mode selectable via keyboard or external input, also during running operation
- Resolution of feed rate display configurable from 0.1 kg/h (0.1 lbs/h) to 1 t/h for batch sizes from some 10 kg/h to 1,000 t/h and more.
- Other features include:
- Options for dynamic adaptation of target feed rate via keyboard or analog input
- Powerful PID controller for tracking the actual flow with reference to target
- Controller parameters can be adjusted during running operation
- Clear operator prompting with display of total quantity, current feed rate, target and chosen product
- Grafic display of relevant process status on color screen.