A Big Bag Filling System is a specialized equipment used in industries to accurately fill large bags (also known as bulk bags, FIBC – Flexible Intermediate Bulk Containers, or super sacks) with bulk materials while monitoring and controlling the weight of the filled bags. These systems are commonly used in industries such as agriculture, construction, chemicals, minerals, food processing, and more.
Here’s how a Big Bag Filling System works and its significance in industries:
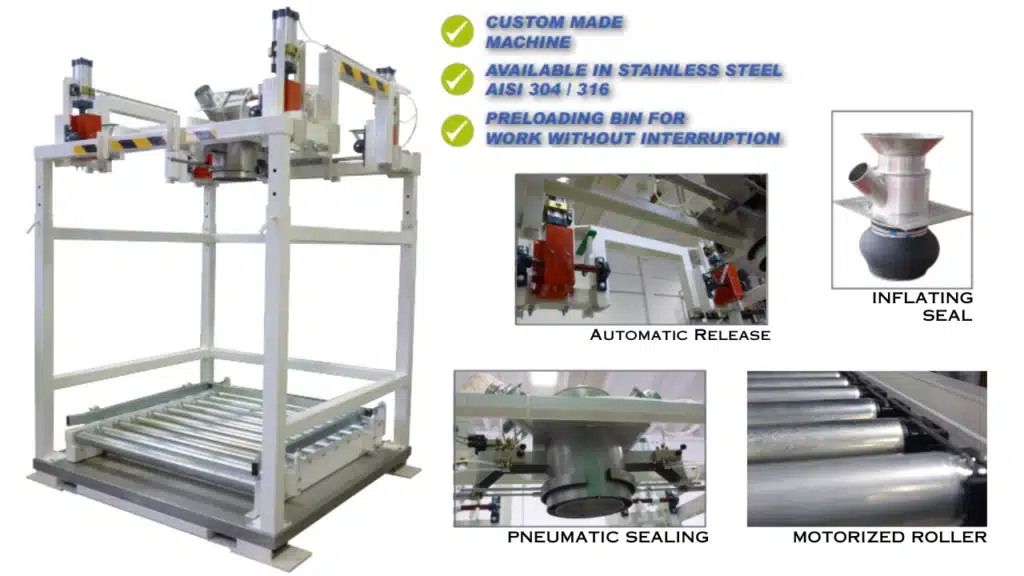
Working Principle: The working principle of a Big Bag Filling System involves the precise measurement of the material being loaded into a bulk bag. The system ensures that the bag is filled to the desired weight by controlling the flow of material into the bag.
The basic components of a Big Bag Filling System include:
- Bulk Material Inlet: The bulk material to be filled into the bag is introduced into the system. This can be done through a hopper, conveyor, or other feeding mechanisms.
- Weighing Platform or Load Cells: The bag is placed on a weighing platform or suspended using load cells. These sensors measure the weight of the bag and its contents in real time.
- Bag Clamping and Inlet Mechanism: The bag is securely clamped onto the filling spout, which is connected to the outlet of the feeding mechanism. The inlet mechanism controls the flow of material into the bag.
- Controller: A controller manages the overall operation of the system. It receives weight data from the load cells and adjusts the flow rate of material to achieve the desired bag weight.
- Cutoff Mechanism: As the bag approaches the target weight, the cutoff mechanism slows down or stops the material flow to prevent overfilling.
- Bag Release: Once the bag is filled to the desired weight, it is released from the filling spout. Some systems may include automatic bag release mechanisms.
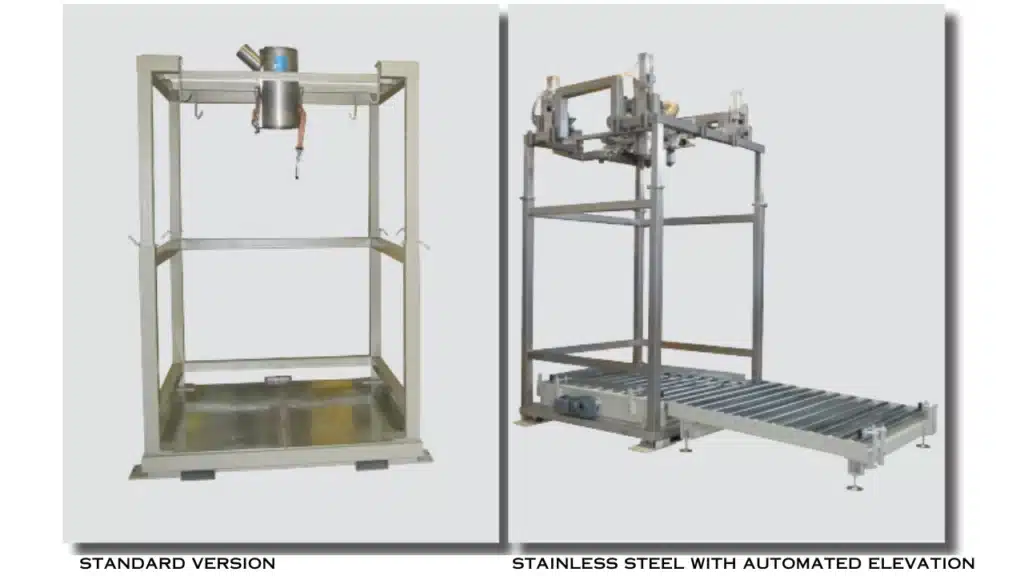
Importance in Industries: Big Bag Filling Systems offer several advantages to industries:
- Accuracy and Precision: These systems ensure that each bag is filled to the exact weight required, minimizing material waste and optimizing material usage.
- Efficiency: Big Bag Filling Weighing Systems automate the bag-filling process, reducing the need for manual labor and improving operational efficiency.
- Consistency: By maintaining uniform bag weights, these systems contribute to consistent product quality and packaging.
- Safety: Automated systems reduce the risk of worker injury associated with manual bag filling. Additionally, features like bag clamping and cutoff mechanisms enhance operator safety.
- Inventory Management: These systems provide accurate data on material consumption, helping with inventory tracking, planning, and management.
- Regulatory Compliance: Precise weighing and documentation provided by these systems aid in meeting regulatory standards and quality control requirements.
- Versatility: Big Bag Filling Weighing Systems can be adapted to handle a wide range of bulk materials, making them suitable for diverse industries.
- Data Collection and Integration: Many modern systems offer data collection, storage, and integration capabilities, allowing for process monitoring, reporting, and analysis.
In summary, Big Bag Filling Systems are essential for industries that need to efficiently and accurately fill large bags with bulk materials. They play a critical role in optimizing operations, reducing waste, and ensuring product quality and consistency.