Pneumatic transport consists in conveying dry powders and granular solids into pipes by means of a gas flow, usually air. Based on the material to air ratio, they are classified as “dense”, “semi-dense” or “dilute” phase systems.
The suction or vacuum systems utilise the vacuum created in the pipe to transfer the material. Pressurised systems, on the other hand, utilise a positive pressure to push the material along the pipe. The many features of the pneumatic transport provide numerous industries with the possibility to convey products without dispersion of the material into the environment. Itineraries can be chosen so that obstacles are avoided with transport on several levels and between different structures.
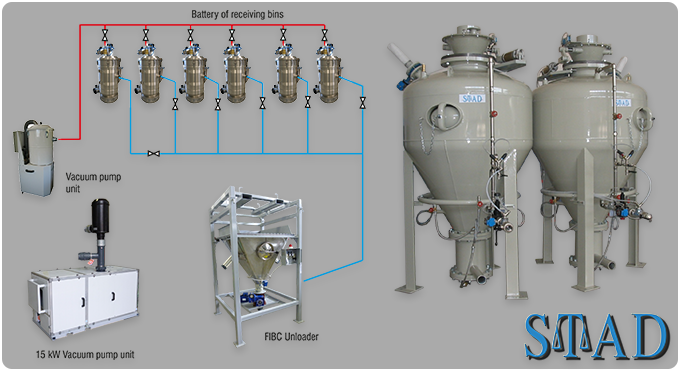
DILUTE PHASE TRANSPORT
Dilute phase transport is characterised by a high transfer speed where the materials “float” in the air stream. The pressure (or vacuum) is relatively low (compared to dense phase systems).
DENSE / SEMI-DENSE PHASE TRANSPORT
Dense Phase transport is commonly used when materials are abrasive or fragile. Dense phase systems operate at a lower transfer speed, at higher pressures and with higher air to product ratios. The higher pressure available permits a longer transport distance.
Semi-dense Phase transport is a phase between dense and dilute. The semi-dense phase systems operate at lower transfer speeds than dilute phase with medium pressures and specific air to product ratios.
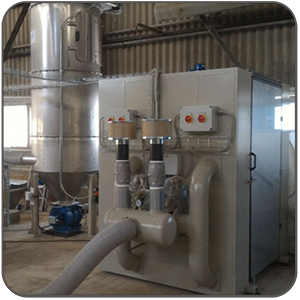
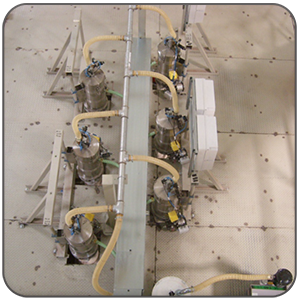
Working Principle:
Material Loading: The bulk material is introduced into the system at the material source, often with the help of feeding devices like rotary valves or screw feeders.
Conveying Air Generation: Compressed air or gas is supplied by a compressor and injected into the pipeline. This creates an air stream with a high velocity.
Material Conveying: The high-velocity air stream entrains the material particles and carries them through the pipeline in a suspended state.
Material Separation: At the material receiver, the conveying air is slowed down, allowing the material to settle out of the air stream and be collected in a hopper or container.
Air Filtration: Before being released into the atmosphere or recirculated, the conveying air is passed through filters to remove any fine particles or dust.
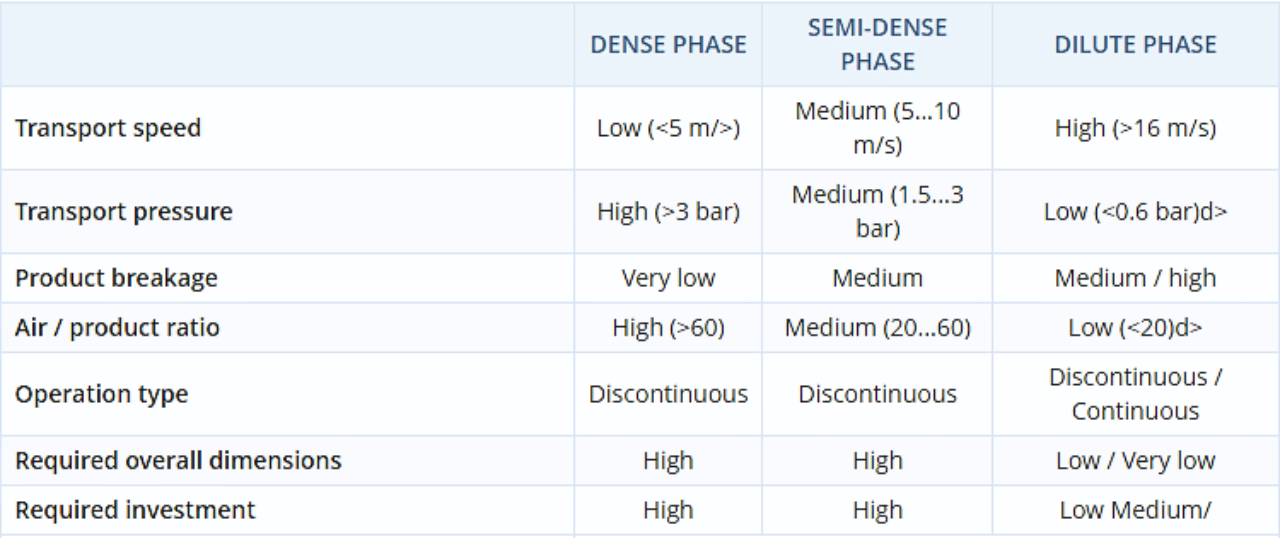
Advantages of Pneumatic Transport Systems:
Dust-Free Transport: Pneumatic systems are excellent for transporting dusty or powdery materials, reducing airborne particles in the facility.
Reduced Contamination: Because there is no physical contact with mechanical parts, the risk of contamination is minimized.
Efficiency: Pneumatic systems are efficient for transporting materials over long distances, around obstacles, and to multiple destinations.
Automation: These systems can be fully automated, reducing the need for manual labor in material handling.
Space Savings: Pneumatic systems require less floor space compared to mechanical conveyors.
Gentle Handling: Pneumatic conveying is gentle on fragile or sensitive materials, minimizing degradation.
Flexibility: Pneumatic systems can be customized to accommodate different material types, flow rates, and distances.
Safety: Personnel exposure to hazardous materials is minimized due to closed-loop transportation.
However, designing and implementing a pneumatic transport system requires careful consideration of factors such as material characteristics, pipeline layout, air pressure requirements, filtration, and safety protocols. The choice of system components and configurations should align with the specific material handling needs of the industry.