A Liquid Dosing System is a specialized technology used in industries to accurately measure and dispense liquid substances. This system is crucial in various industries such as pharmaceuticals, food and beverage, chemicals, cosmetics, and more, where precise and controlled dosing of liquids is essential for product quality, safety, and compliance.
Here’s an overview of how a Liquid Dosing Weighing System works and its components:
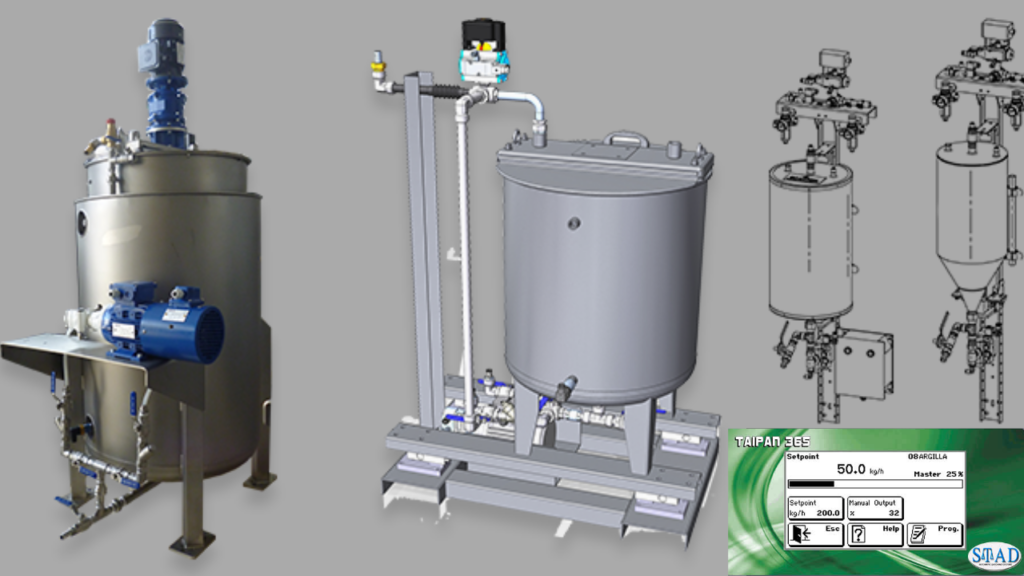
Components of a Liquid Dosing System:
Storage Tanks or Containers: These hold the liquid substances that need to be dosed. They are often equipped with sensors to monitor the liquid level.
Weighing Platform: A sturdy platform that supports the containers or tanks and accurately measures the weight of the liquid.
Load Cells: These are sensors placed under the weighing platform to measure the weight of the liquid. They provide real-time feedback to the system’s controller.
Pumps or Valves: These are responsible for controlling the flow of liquid from the storage tank to the dosing container. They are often automated and precisely controlled.
Dosing Containers: These containers hold the exact quantity of liquid required for a specific batch or process. They are placed on the weighing platform during dosing.
Batching Controller: An interface device that allows operators to set dosing parameters, monitor the dosing process, and receive alerts or notifications.
Sensors and Feedback Mechanisms: These include sensors for detecting the dosing container’s presence, liquid level sensors, and feedback mechanisms to ensure accurate dosing and prevent overflows.
Working Principle:
The operator sets the desired dosing parameters through the HMI, such as the target weight, dosing speed, and tolerances.
The system confirms the availability of an empty dosing container on the weighing platform.
The system starts the dosing process by opening the valve or activating the pump, allowing the liquid to flow from the storage tank into the dosing container.
The load cells continuously measure the weight of the dosing container and its contents in real-time.
The control system calculates the dosed weight based on the weight increase and compares it to the desired target weight.
As the dosing container approaches the target weight, the system slows down the flow rate to achieve precise dosing.
Once the target weight is reached, the system stops the flow of liquid and alerts the operator or proceeds with the next step in the manufacturing process.
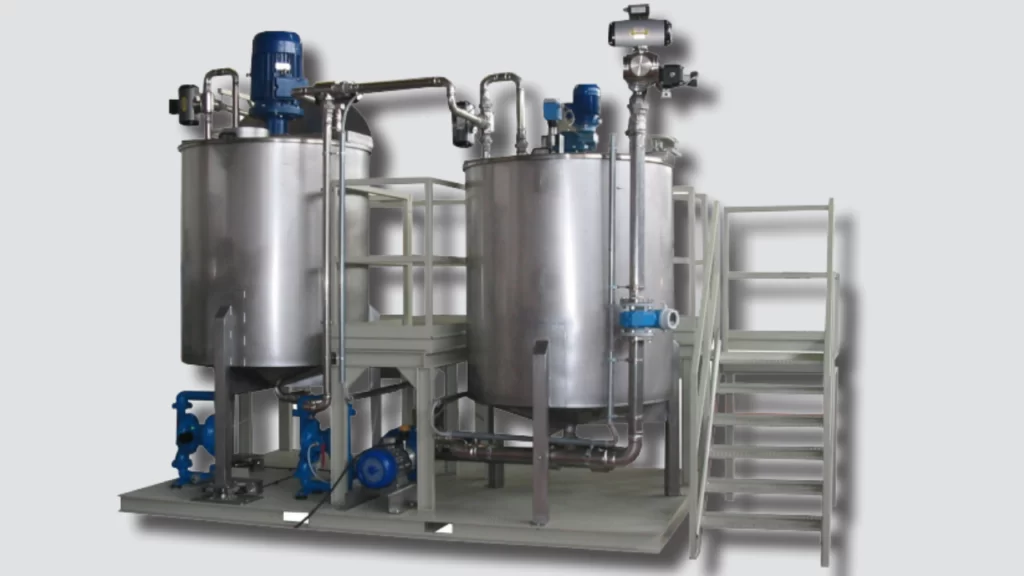
Benefits:
Accuracy: Ensures precise dosing, reducing material waste and improving product quality.
Automation: Reduces manual intervention, improving consistency and efficiency.
Traceability: Provides data logging for compliance with regulations and quality control.
Time Savings: Faster dosing process compared to manual methods.
Reduced Contamination: Minimizes human contact with the substance, important for industries with strict hygiene requirements.
Flexibility: Can handle various liquid substances and dosing quantities.
Liquid Dosing Systems play a critical role in industries where small variations in liquid dosing can have significant impacts on product quality, safety, and cost-effectiveness. They contribute to the overall optimization of manufacturing processes while maintaining stringent quality control standards.