Weighing systems are critical in the pharmaceutical industry to ensure accurate measurement, quality control, regulatory compliance, and patient safety. The pharmaceutical industry deals with highly regulated and sensitive materials, and precise weighing is essential for producing safe and effective medications.
Here’s how weighing systems are used in the pharmaceutical industry:
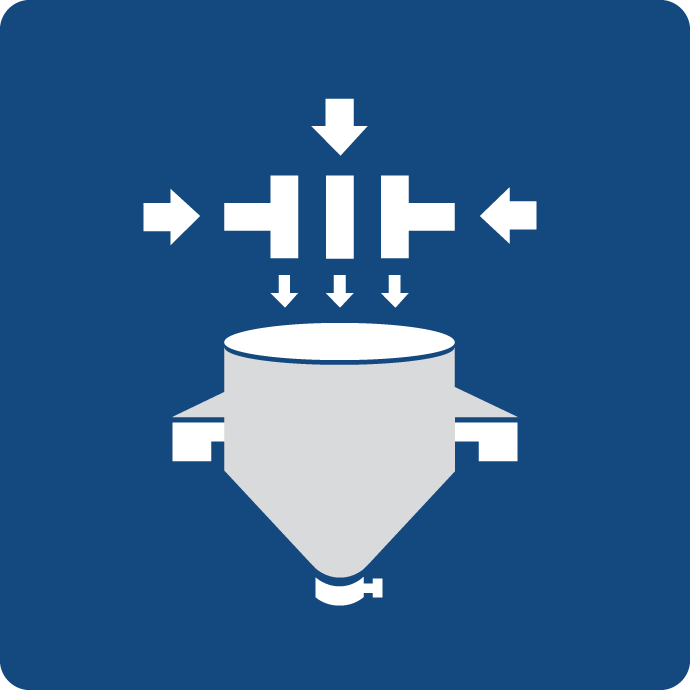
Batching & Mixing System
Active Pharmaceutical Ingredients (APIs) Preparation. Pharmaceutical manufacturers require precise measurement of APIs for drug formulation. These systems ensure accurate measurement and dispensing of APIs, excipients, and other ingredients during drug formulation.
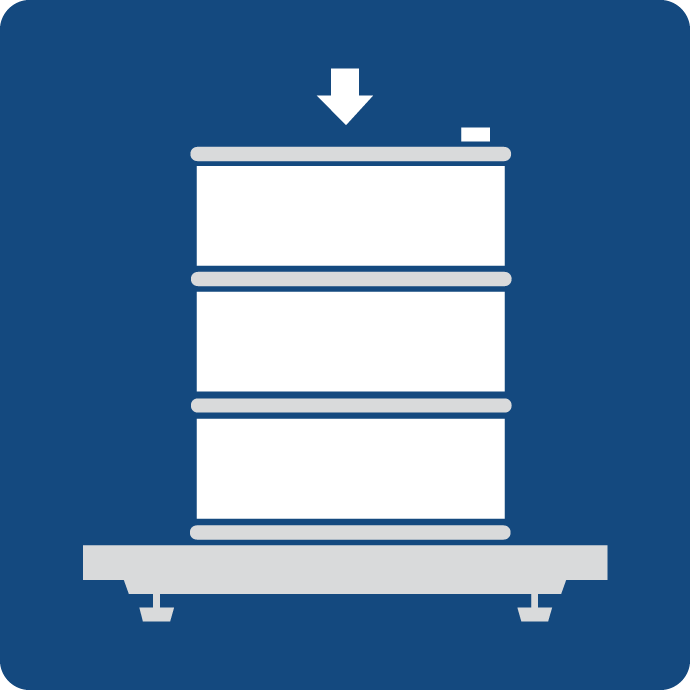
Liquid Dosing System
Liquid pharmaceutical formulations require accurate measurement to ensure proper dosing. These systems accurately fill containers with liquid medications at the correct volume.
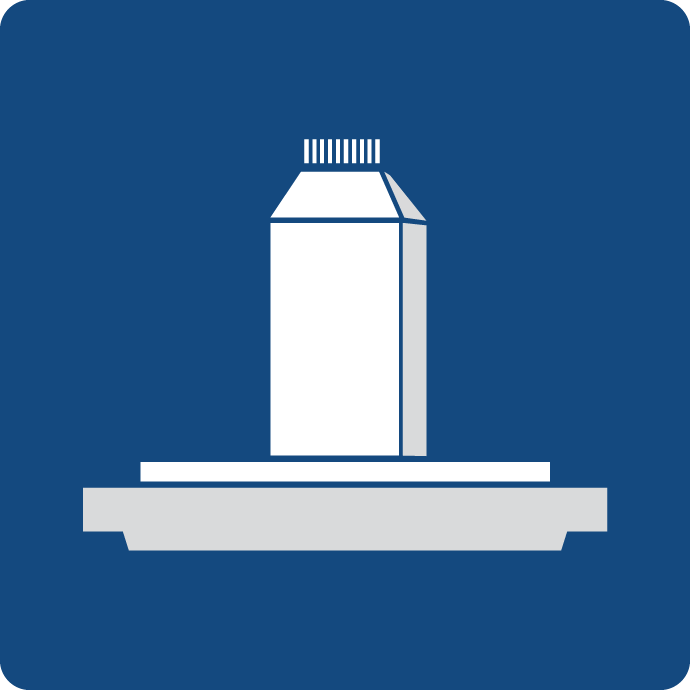
Laboratory Balances
Precise measurements are essential during drug development and testing for R&D (Research & Development) department. High-precision lab balances are used for accurate measurements in research and development settings.
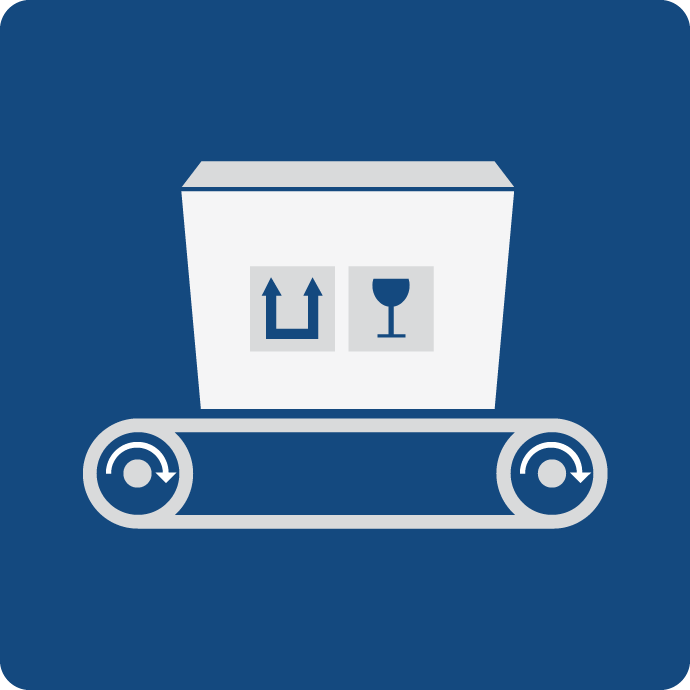
Checkweigher
Proper packaging is crucial to prevent contamination and ensure accurate dosing. These systems verify the weight of packaged products to prevent underfilling or overfilling.
Benefits of Weighing Systems in the Pharmaceutical Industry:
Patient Safety: Accurate weighing ensures proper dosing of medications, enhancing patient safety.
Quality Assurance: Precise measurement maintains consistent product quality.
Regulatory Compliance: Compliance with regulations ensures safe and effective medications.
Cost Control: Accurate weighing helps control costs and prevents material wastage.
Inventory Management: Accurate inventory data assists in production planning and waste reduction.
Efficiency: Automated weighing processes improve process efficiency and reduce manual labor.
Traceability: Integrated systems ensure accurate traceability of ingredients and products.
When implementing weighing systems in the pharmaceutical industry, it’s essential to choose equipment that adheres to industry regulations, meets hygiene standards, and provides accuracy and reliability. Regular calibration, maintenance, and adherence to strict protocols are necessary to ensure accurate and consistent performance.