A weighing system in a power plant is crucial for accurate measurement of materials, such as coal, biomass, fuel oil, and other components, that are used in various processes within the plant. These systems ensure efficient operation, precise inventory management, and compliance with environmental and safety regulations.
Here’s an overview of the weighing systems commonly used in power plants:
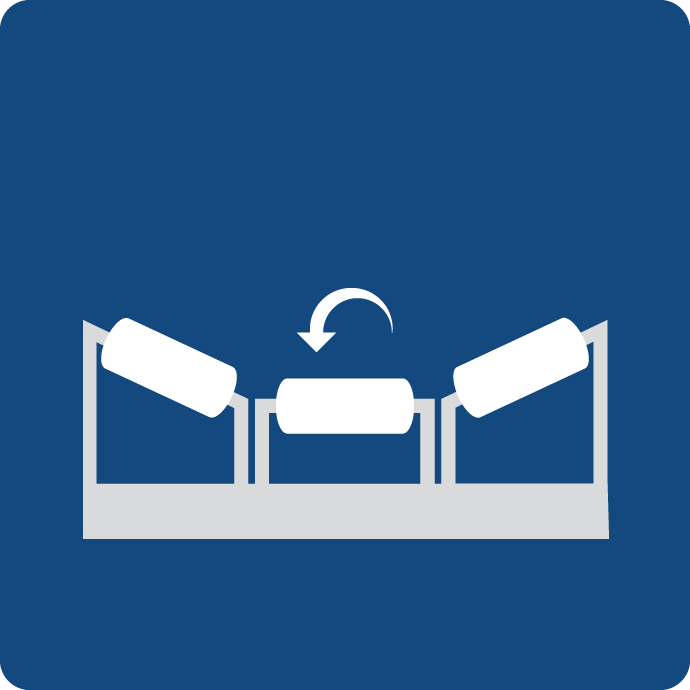
Belt Scale
These systems are used to measure the flow rate and total amount of material transported on conveyor belts. They are commonly employed to measure the coal flow to boilers, ensuring that the correct amount of fuel is being supplied for combustion. Belt scales can provide continuous and accurate measurements.
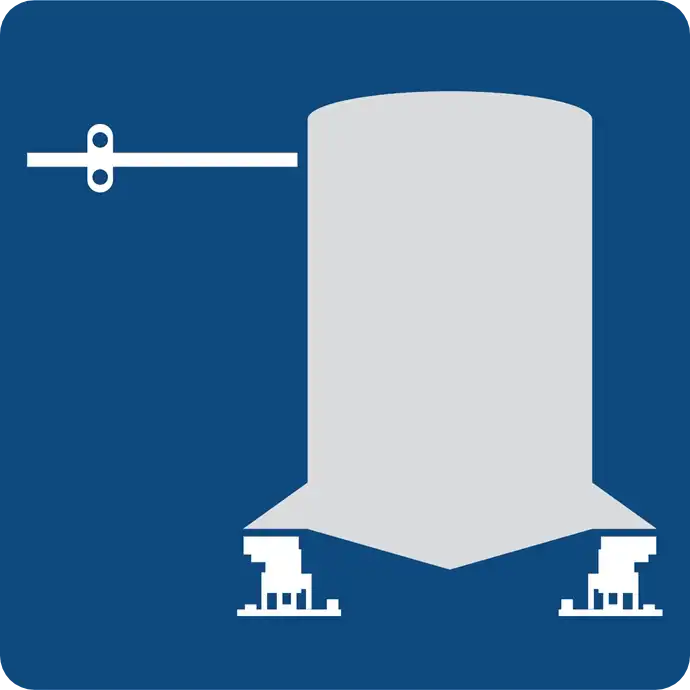
Hopper & Silo Weighing
In power plants, materials are often stored in hoppers or silos before being fed into various processes. Weighing systems can be integrated into these storage containers to monitor the amount of material inside. This ensures that the correct amount is available for processing and prevents overfilling.
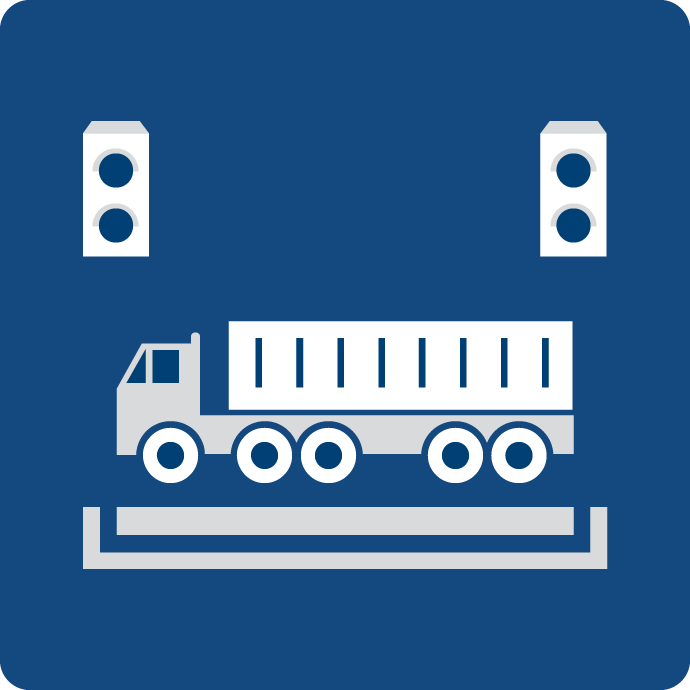
Truck Scale
Power plants may receive materials such as coal or biomass via trucks or railcars. Weighbridges or railcar weighing systems are used to measure the weight of these vehicles before and after loading or unloading. This provides accurate data for inventory management and billing purposes.
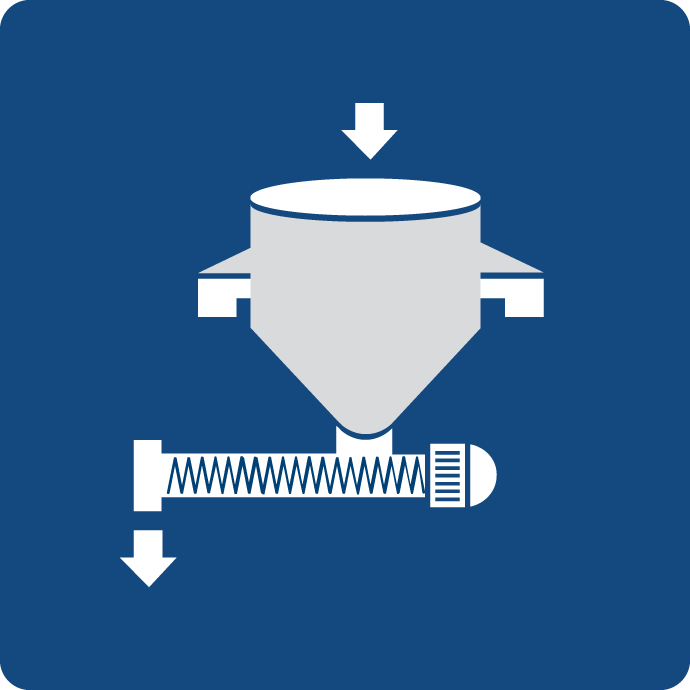
Weighing Feeder
Weigh feeders help regulate the amount of fuel supplied to the combustion process. This ensures stable and controlled combustion, preventing excessive fuel consumption and reducing the risk of furnace explosions.
Choosing the appropriate weighing system depends on the specific needs of the power plant, the type of materials being handled, and the level of accuracy required. Proper installation, calibration, and maintenance are key to ensuring the reliability and accuracy of the weighing systems in a power plant.