Panatronik provides solutions for automatic batching systems. Be it a new automatic batching system requirement or automating the existing manual batching system, we fulfill both the requirements.
Batching is one of the major and vital parts of many industries. That’s why Panatronik plays a very vital role in maintaining the quality as well as quantity of the output of a plant. Batching is taking different materials in different quantities and mixing them together to make a raw mix or a final product.
Panatronik provides the system from single ingredient to multi-ingredient with base batching system to multi complex batching system.
LAUMAS W-SERIES weight indicators have several operating programs (firmware) available that can be installed on the instrument according to different needs.
Benefits:
Precision: Ensures accurate and consistent batch weights, reducing material waste and product variability.
Efficiency: Automates the batch loading process, increasing production throughput and reducing labor requirements.
Quality Control: Maintains product quality and regulatory compliance by consistently achieving target batch weights.
Data Recording: Records batch information, weight data, and loading times, enabling detailed quality control and traceability.
Flexibility: Can be adapted to various material types, batch sizes, and production requirements.
Process Integration: Seamlessly integrates with other production processes to optimize workflow.
Cost Savings: Minimizes material waste and improves resource utilization, leading to cost savings over time.
How to choose the right program to use?
Here are the key features of each firmware and when to use them.
BASE
This is the simplest program and is installed by default on our weight indicators.
The base firmware allows set-point values to be set freely but does not have specific automatic batching functions.

It is ideal in situations where the instrument simply needs to display the weight and put it at the service of the weighing application in which it is installed.
Weight indicators with base firmware can be connected via fieldbus or analog output to the PLC that manages the automation of the machine or system on which the weighing system is installed.
With the BASE program, it is possible to carry out also manual or semi-automatic batching, thanks to the NET/GROSS function, using the corresponding external input or the TARE button on the weight indicator.
This button is used to toggle between the two states and to display both the net weight of the product in the phase of batching and the gross weight present on the system.
RIP
The RIP firmware transforms the instrument into a serial remote display that displays the weight value transmitted by a second weight indicator that is actually connected to one or more load cells.
It is useful for displaying the same weight measured by a single weighing system on two different instruments.
On the instrument working as a remote display, you can determine which type of weight is displayed (gross or net) and you can set setpoints to pair with the digital outputs.

LOAD
A batch weighing system is a specialized technology used in various industries to accurately measure and control the weight of materials or products that are loaded in batches. This system ensures that each batch meets specific weight requirements, which is crucial for quality control, regulatory compliance, and efficient production processes.
UNLOAD
This is the single-product unload batching program, for automatic batching applications.
It is used in processes where a predetermined quantity of product has to be batched, automatically extracted from the weighing system.
It is useful for example in big bag emptier machines, among other functions also to keep in memory the remaining part of product to be batched when unloading once the big bag has been completely emptied and has to be replaced with a new one (big bag emptying function)
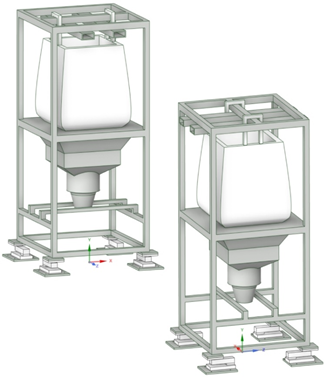
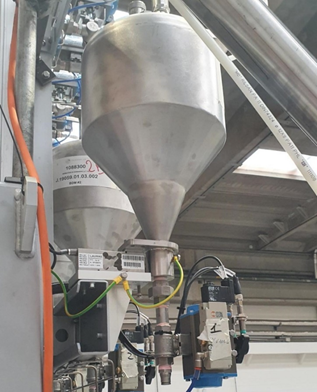
3/6/14 PRODUCTS
This is the multi-product batching firmware, for automatic batching applications.
It allows the weight indicator to manage the batching sequence of a mixture of products automatically loaded into the weighing system.
It is useful, for example, for batching the ingredients used for making concrete
MULTIPROGRAM
This is the firmware that includes all the previous programs.
It is useful for vendors who decide to keep in stock weight indicators whose final application is not yet known: the installer will be able to select the type of software they want, depending on the specific application.
With MULTI-program weight indicators, the vendor will then have “wildcard” instruments at hand to adapt to the different supply needs that will be required.
Batch weighing systems are adaptable to different industries and applications, providing enhanced control over material loading processes and contributing to overall production efficiency and quality.
The power of Weight Transmitter

Weight indicators and weight transmitters are both essential components used in weighing systems, but they serve different purposes and have distinct functionalities within those systems.
Role of a Weight Transmitter in a Batching System:
A weight transmitter serves as a communication bridge between the load cells or weighing sensors and the central control system of the batching process. Its primary function is to amplify, digitize, and transmit the weight signals from the load cells to the control system, enabling accurate weight measurement and control during the batching process.
Functionality of a Weight Transmitter:
Signal Amplification: The signals generated by load cells are very small and require amplification before they can be effectively processed. Weight transmitters include circuitry that amplifies these weak signals to a level that is suitable for further processing.
Analog-to-Digital Conversion: Load cell signals are analog in nature, while modern control systems often work with digital data. Weight transmitters include analog-to-digital converters (ADCs) that convert the amplified analog signals into digital data that can be processed by computers or microcontrollers.
Signal Conditioning: Weight transmitters may include signal conditioning features to enhance the accuracy of the measurement. This can involve compensating for temperature variations, linearity errors, and other factors that might affect the accuracy of the weight measurement.
Digital Communication: The weight transmitter communicates with the central controller using digital communication protocols. Common protocols include RS-232, RS-485, Analog Ouput, Ethernet TCP/IP, or more modern protocols like PROFIBUS, Modbus, EtherCAT, Profinet IO, SercosIII, DeviceNet and many more
Data Transmission: The weight transmitter transmits the digital weight data to the central controller or a supervisory computer system. This real-time data allows the batching system to monitor and control the weight of materials being loaded accurately.
Calibration and Configuration: Weight transmitters often come with built-in calibration and configuration features. This allows operators to calibrate the system and set parameters such as maximum weight limits, zero points, and more.
Benefits of Weight Transmitters in Batching Systems:
Accuracy: Weight transmitters ensure precise weight measurement, leading to accurate batching processes and consistent product quality.
Real-Time Monitoring: They provide real-time weight data to the control system, allowing for immediate adjustments if deviations occur.
Automation: Weight transmitters enable automation by integrating with central control systems, reducing manual intervention and human error.
Data Logging and Reporting: Weight transmitters often include data logging capabilities, allowing for the collection and analysis of weight-related data over time.
Process Optimization: Accurate weight measurement contributes to process optimization, reducing material waste and improving efficiency.
Integration: Weight transmitters can be integrated with other control and automation systems, facilitating seamless communication within the batching process.
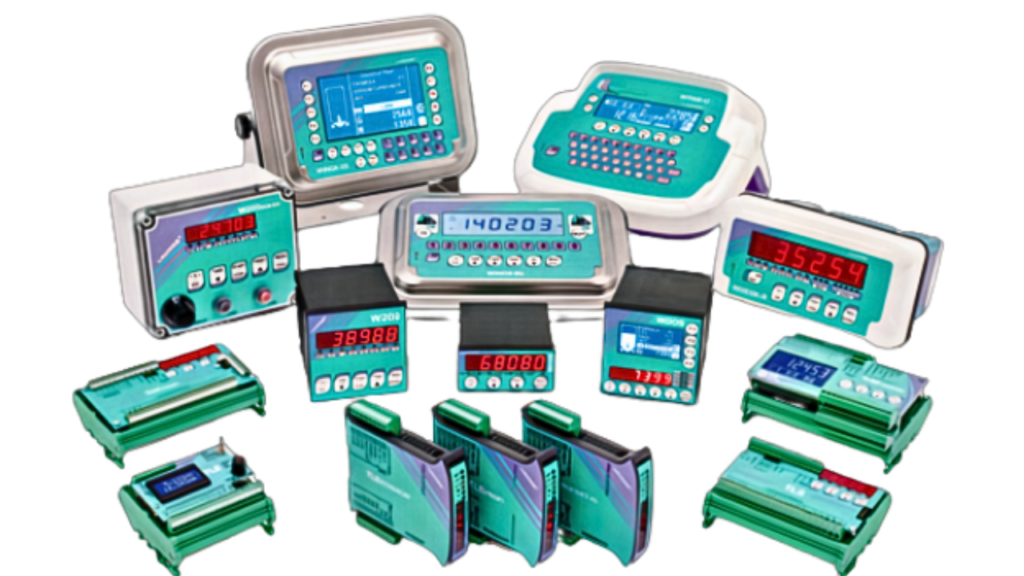
Weight Indicators or Weight Transmitters?
Key Differences:
Primary Function: Weight indicators focus on displaying weight readings to operators, while weight transmitters concentrate on converting and transmitting weight data to external systems.
Operator Interaction: Weight indicators allow for direct interaction with operators, whereas weight transmitters are typically set up and configured for communication with other systems; such as PLC or Scada systems.
Integration: Weight transmitters are more oriented toward seamless integration with control and automation systems, while weight indicators are often standalone devices.
Display: Weight indicators have displays for local weight reading, while weight transmitters might have limited or no display.
In summary, weight indicators are used for local weight monitoring and operator interaction, whereas weight transmitters are used for converting and transmitting weight data to other systems for further processing and automation. The choice between the two depends on the specific requirements of the weighing application and the level of integration with other systems needed.