Glass manufacturers use various types of weighing systems to ensure accurate measurements of raw materials, ingredients, and finished products. The choice of weighing system depends on factors such as the specific production processes, required accuracy, and the scale of operations.
Here are some common types of weighing systems used in glass manufacturing:
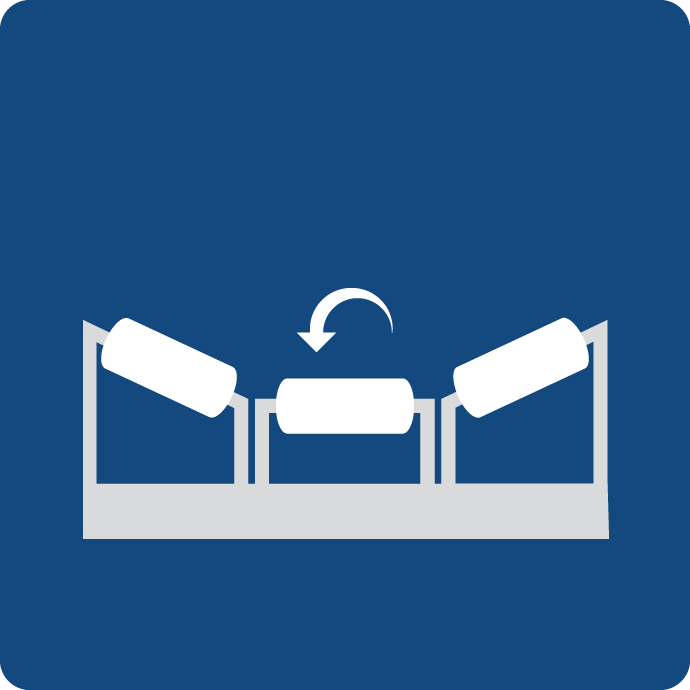
Belt Scale
Belt weighers, also known as belt scales, are used to measure the weight of materials as they move along a conveyor belt. This type of weighing system is often used to monitor the flow of raw materials into the furnace, ensuring consistent charging rates for the melting process.
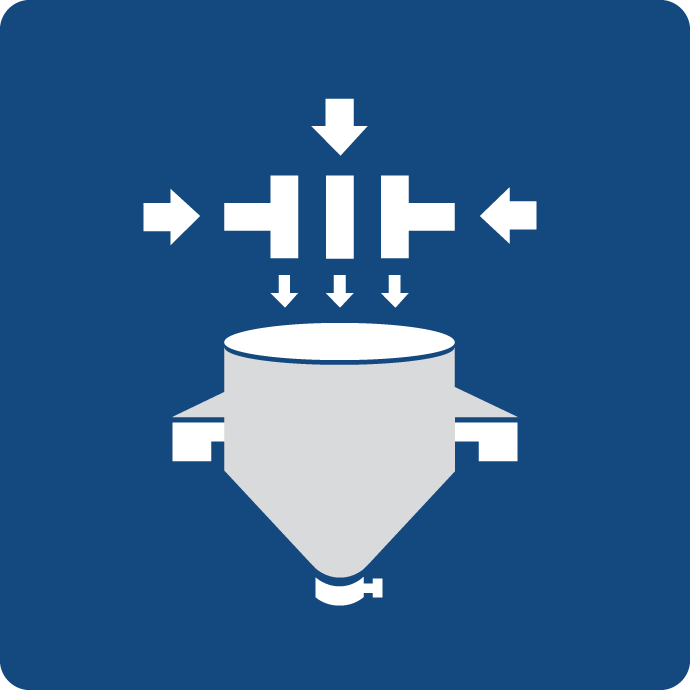
Batching System
Batch weighing systems are designed to accurately measure and dispense specific quantities of various raw materials for mixing. These systems are crucial for maintaining the desired glass composition. They often involve multiple weigh hoppers that dispense materials into a central mixing system, ensuring precise ratios are maintained.
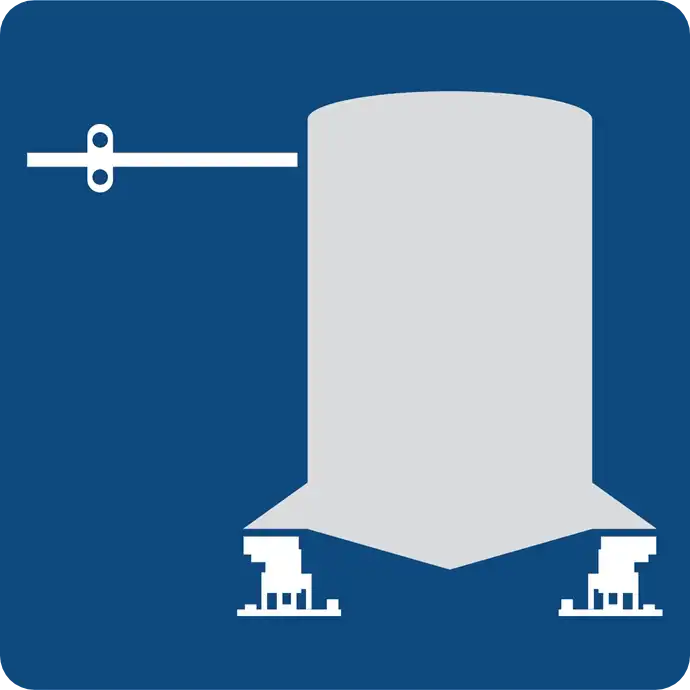
Hopper & Silo Weighing
Hopper and silo weighing systems are used to measure the weight of bulk materials stored in containers such as hoppers and silos. These systems are essential for managing inventory and ensuring that the right amount of raw materials is available for production.
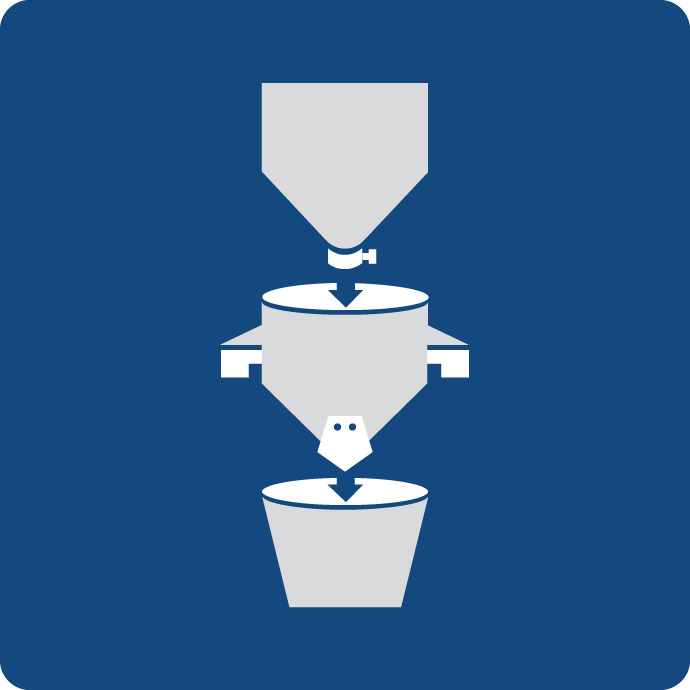
Loss-in-Weight Feeder
Continuous weighing systems are used to monitor and control the flow of materials throughout the production process. These systems can be integrated into conveyors, pipes, and chutes to provide continuous weight measurements. They help maintain consistent material flow rates and ensure accurate input into various manufacturing stages.
When selecting a weighing system for a glass manufacturing process, it’s important to consider factors such as the required accuracy, production volume, material characteristics, and the level of automation desired. Collaborating with Panatronik can help tailor the solution to the specific needs of the glass manufacturing operation.